Caleb DeValve
- Lab Alum
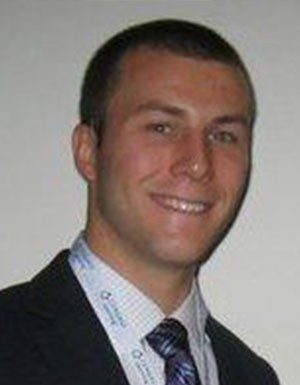
Investigations on Void Formation in Composite Molding Processes and Structural Damping in Fiber-Reinforced Composites with Nanoscale Reinforcements
Fiber-reinforced composites (FRCs) offer a stronger and lighter weight alternative to traditional materials used in engineering components such as wind turbine blades and rotorcraft structures. Composites for these applications are often fabricated using liquid molding techniques, such as injection molding or resin transfer molding. One significant issue during these processing methods is void formation due to incomplete wet-out of the resin within the fiber preform, resulting in discontinuous material properties and localized failure zones in the material. A fundamental understanding of the resin evolution during processing is essential to designing processing conditions for void-free filling, which is the first objective of the dissertation. Secondly, FRCs used in rotorcraft experience severe vibrational loads during service, and improved damping characteristics of the composite structure are desirable. To this end, a second goal is to explore the use of matrix-embedded nanoscale reinforcements to augment the inherent damping capabilities in FRCs.
The first objective is addressed through a computational modeling and simulation of the infiltrating dual-scale resin flow through the micro-architectures of woven fibrous preforms, accounting for the capillary effects within the fiber bundles. An analytical model is developed for the longitudinal permeability of flow through fibrous bundles and applied to simulations which provide detailed predictions of local air entrapment locations as the resin permeates the preform. Generalized design plots are presented for predicting the void content and processing time in terms of the Capillary and Reynolds Numbers governing the molding process.
The second portion of the research investigates the damping enhancement provided to FRC\'s in static and rotational configurations by different types and weight fractions of matrix-embedded carbon nanotubes (CNTs) in high fiber volume fraction composites. The damping is measured using dynamic mechanical analysis (DMA) and modal analysis techniques, and the results show that the addition of CNTs can increase the material damping by up to 130%. Numerical simulations are conducted to explore the CNT vibration damping effects in rotating composite structures, and demonstrate that the vibration settling times and the maximum displacement amplitudes of the different structures may be reduced by up to 72% and 50%, respectively, with the addition of CNTs.
Publications
- C-10-01: C.DeValve and R. Pitchumani, “Void Formation During Preform Impregnation in Liquid Composite Molding Processes,” Paper No. 1, Proceedings of the 10th International Conference on Flow Processes in Composite Materials, Ascona, Switzerland, July 11-15, 2010, 5 pp., 2010.
- C-11-01: C. DeValve and R. Pitchumani, "A Numerical Simulation of Air Entrapment during Resin Transfer Molding," Proceedings of SAMPE 2011, Long Beach, California, May 23-26, 2011, 14 pp., 2011.
- C-11-03: C. DeValve and R. Goff, "Integrating Emerging Technologies with Undergraduate Engineering Design Courses," Proceedings of 118th Annual ASEE Conference, Vancouver, B.C. Canada, June 26-29, 2011, 16 pp., 2011.
- C-13-01: C. DeValve, N. Ameri, P. Tarazaga, and R. Pitchumani, "Modal analysis of rotating carbon nanotube infused composite beams," Paper No. 110, IMAC XXXI AConference and Exposition on Structural Dynamics, Feb 11-14, 2013, Garden Grove, CA.
- J-12-02: C. DeValve and R. Pitchumani, "An Analytical Model for the Longitudinal Permeability of Aligned Fibrous Media," Composites Science and Technology, 72(13),1500-1507, 2012.
- J-13-03: C. DeValve and R. Pitchumani, “Simulation of Void Formation in Liquid Composite Molding Processes,”Composites A: Applied Science and Manufacturing, 51, 22-32, 2013.
- J-13-04: C. DeValve and R. Pitchumani, “A Numerical Analysis of Carbon Nanotube based Damping in Rotating Composite Structures,”Composite Structures, 103, 18-26, 2013.
- J-13-05: C. DeValve and R. Pitchumani, “Experimental Investigation of the Damping Enhancement in Fiber-reinforced Composites with Carbon Nanotubes,” Carbon, 400-415, 2013.
- J-14-06: C. DeValve and R. Pitchumani, “Analysis of Vibration Damping in a Rotating Composite Beam with Embedded Carbon Nanotubes,” Composite Structures, 110,289-296, 2014, 2014