Yan Xiao
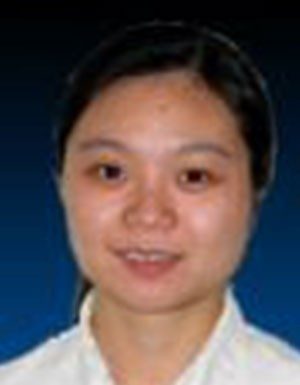
Research Projects
A Generalized Analysis of Capillary Flows in Microscale Channels and Tubes
Investigations on the motion of a fluid in capillary geometries have been extensively reported in the literature using both experimental and theoretical approaches. Based on different types of fluids, geometric configurations, and model assumptions, theoretical analyses lead to a number of first or second-order nonlinear ordinary differential equations for the fluid flow dynamics. Owing to the nonlinear characteristics, most studies resort to numerical solutions to the governing equations. In this work, the theories for capillary flow are generalized to a unified differential equation which includes the effects of the entrance, the inertial forces, and the dynamic contact angle. An analytical solution of the differential equation is obtained using a double Dirichlet series. The readily evaluated analytical solution is compared with experimental and numerical results in the literature, and is shown to predict capillary flows for a wide range of fluids and microchannel and tube geometries in a unified manner.
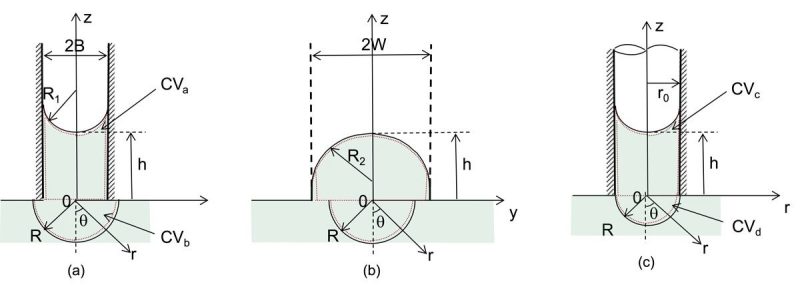
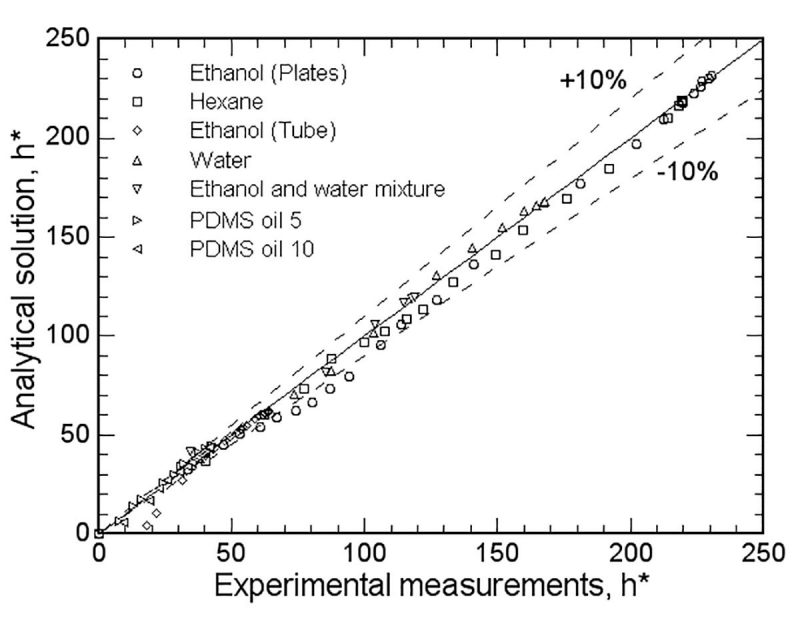
Capillary-driven Nanoparticulate Slurry Flow during a Micromold Filling Process
The microcasting technique for the fabrication of microstructures mainly involves two consecutive steps, namely, the capillary-driven flow of nanoparticulate slurry in micromolds and sintering of the resulting preform. During the mold-filling step, particle settling leads to a spatial particle distribution in the preform, which affects the subsequent sintering kinetics, and in turn, and causes a shape distortion in the final sintered product. This work presents a comprehensive theoretical model which is adopted to account for the capillary-driven flow and simultaneous particle settling behavior during the filling step. Numerical simulations are performed over a wide range of parameters to illustrate the effects of four nondimensional groups on the fill time and particle distribution, and to develop design windows, which may serve as guidelines in the design of particle properties, slurry composition, and mold dimensions to maintain a desired level of homogeneity in particle distribution.
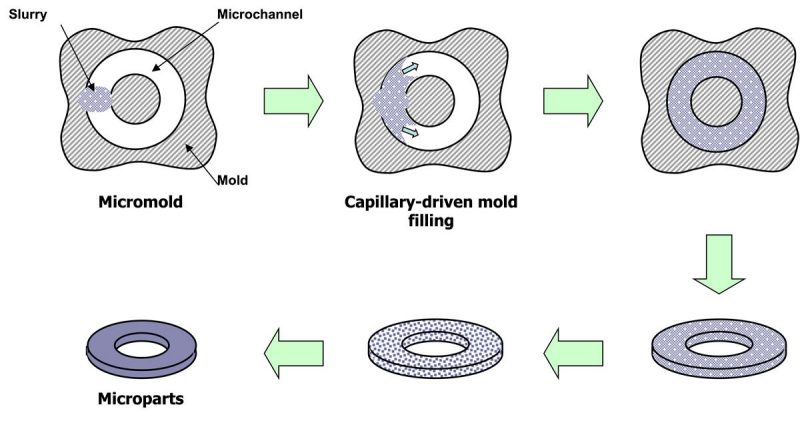
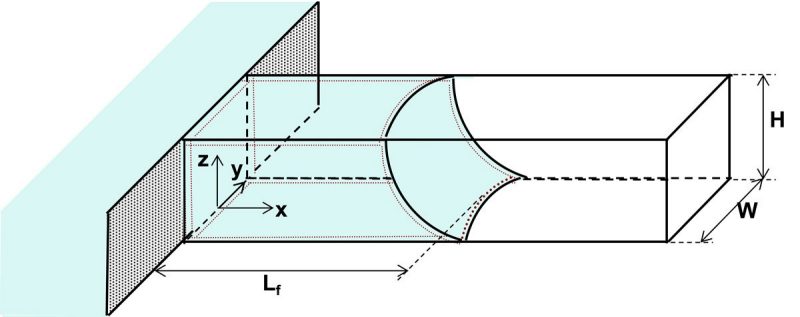
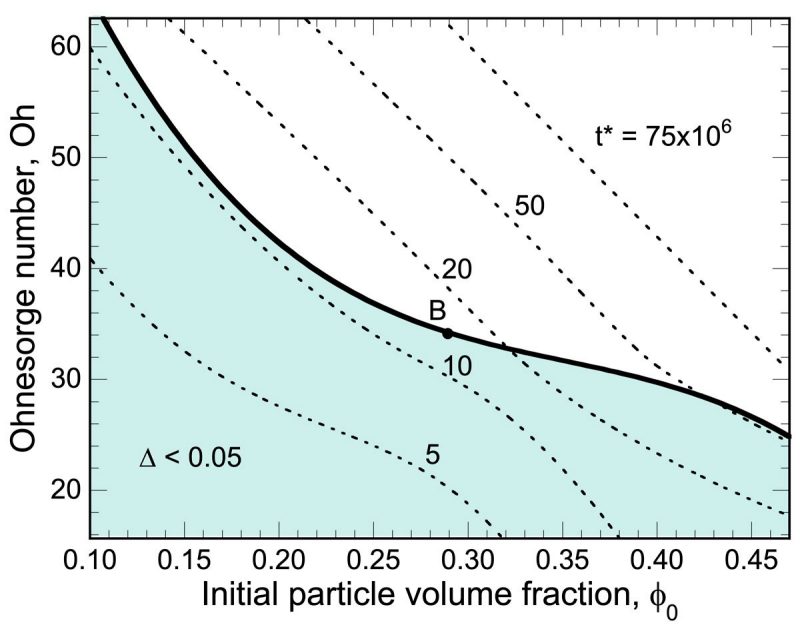
Publications
- A. Mawardi, Y. Xiao and R. Pitchumani, “Theoretical Analysis of Capillary-driven Nanoparticulate Slurry Flow During a Micromold Filling Process,” International Journal of Multiphase Flow, 34(3), 227–240, 2008.
- Y. Xiao, F. Yang, and R. Pitchumani, “A Generalized Analysis of Capillary Flows in Channels,” J. Colloid and Interface Science, 298(2), 880–888, 2006.
- Y. Xiao, A. Mawardi and R. Pitchumani, “Flow of Nanoparticulate Slurry During a Microcasting Process for the Fabrication of Metallic and Ceramic Microstructures,” in Proceedings of the 13th International Heat Transfer Conference, August 13–18, 2006, Sydney, Australia, Paper No. NAN-04, 12 pp. ISBN 1-56700-226-9, Begell House, Inc., Redding, CT.
Sponsor
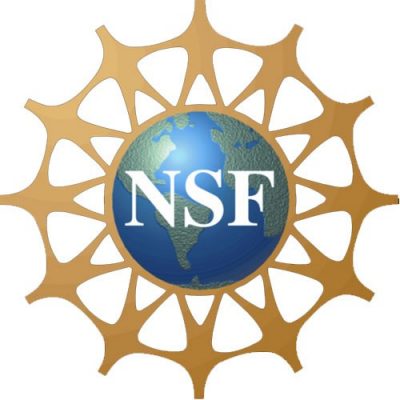